Packaging Machine Repair Service: Quick and Affordable Solutions for Your Business
Comprehending the Key Elements and Repair Service Strategies for Packaging Device Maintenance
Effective maintenance of packaging machines pivots on a thorough understanding of their vital elements, including the framework, drive system, and securing mechanisms. Recognizing usual maintenance problems, paired with the application of preventative techniques and fixing techniques, can substantially enhance machine reliability.
Trick Parts of Packaging Devices
Product packaging makers contain several crucial elements that function together to ensure effective and efficient packaging procedures. At the core of these devices is the framework, which gives architectural honesty and houses the different operating parts. The drive system, frequently a combination of electric motors and equipments, promotes the activity of elements, enabling exact operation throughout the packaging cycle.
One more essential element is the conveyor system, which moves items through various phases of the packaging procedure. This is often complemented by sensors and controls that keep track of the position and rate of items, making sure synchronization and lessening errors. The loading system is important for precisely dispensing the right amount of product into plans, whether in liquid, powder, or strong type.
Sealing devices, including heat sealants or adhesive applicators, play an essential function in protecting plans, stopping contamination and prolonging rack life. Furthermore, identifying systems are essential for giving needed product details, making certain compliance with regulations. The control panel, outfitted with easy to use interfaces, enables operators to handle device functions, screen efficiency, and make adjustments as required, making certain optimal performance and performance in packaging operations.
Usual Maintenance Problems
Reliable operation of packaging equipments relies heavily on routine upkeep to prevent usual issues that can interrupt manufacturing. Amongst these issues, mechanical wear and tear is prevalent, specifically in elements like electric motors, conveyors, and seals, which can result in unforeseen downtimes. Furthermore, imbalance of components can cause ineffective procedure, triggering items to be inaccurately packaged or harmed during the process.
One more usual upkeep problem entails the buildup of dust and particles, which can hinder the equipment's sensing units and relocating components. packaging machine repair service. This not just influences efficiency yet can likewise position safety and security risks. Additionally, lubrication failures can cause increased friction, resulting in getting too hot and ultimate part failing.
Electrical issues, typically coming from loose links or worn-out circuitry, can disrupt equipment functions, resulting in considerable production hold-ups. Last but not least, software problems as a result of improper arrangements or outdated programs can hinder the equipment's procedure, requiring immediate treatment. Resolving these typical maintenance problems proactively is vital for ensuring optimum performance and long life of packaging equipment.
Preventative Maintenance Approaches
Executing preventative maintenance strategies is critical for sustaining the performance and reliability of product packaging machines. These methods encompass a methodical approach to maintenance, concentrating on the regular assessment and servicing of devices to preempt possible failures. By adhering to a set up upkeep program, operators can determine damage on components prior to they bring about considerable failures.
Trick elements of a preventative maintenance method consist of regular evaluations, cleansing, component, and lubrication substitutes based upon manufacturer referrals. Using lists can simplify this procedure, ensuring that no vital jobs are forgotten. Furthermore, keeping exact documents of upkeep tasks help in tracking the machine's performance over time, helping with informed decision-making regarding future upkeep needs.
Training staff on the significance of preventative upkeep boosts compliance and promotes a culture of proactive care. Implementing a predictive upkeep component, making use of information analytics and use this link sensing unit innovation, can additionally enhance equipment efficiency by forecasting failings before they occur.
Repairing Methods
When confronted with breakdowns or inadequacies in packaging machines, utilizing systematic troubleshooting strategies is crucial for determining and fixing issues promptly. The primary step in reliable troubleshooting is to establish a clear understanding of the device's functional parameters and efficiency metrics. This includes assessing the maker's specifications, along with any mistake alerts or codes presented.
Next, drivers should carry out an aesthetic assessment, checking for evident indicators of damage, wear, or imbalance. This frequently consists of analyzing equipments, sensors, and belts to pinpoint prospective reasons for malfunction. Gathering functional information, such as production rates and downtime logs, can likewise give insights into persisting concerns.
Once prospective issues are recognized, using a rational technique to isolate the origin is important. This might call for screening private parts or systems in a regulated way. Participating in conversations with operators who interact with the machinery consistently can yield useful responses concerning unusual habits or patterns.
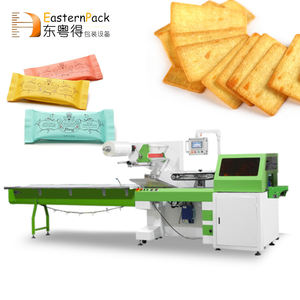
Repair Service and Replacement Ideal Practices
A thorough understanding of repair service and replacement ideal methods is important for keeping the durability and performance of packaging machines. Routinely assessing the problem of device parts permits timely treatment, stopping even more considerable issues that can bring about costly downtimes.
When repair work are needed, it is necessary to utilize OEM (Original Tools Manufacturer) components to ensure compatibility and performance. This not only maintains the honesty of the maker but likewise upholds guarantee contracts. In addition, it is recommended to keep an inventory of important spare parts to promote fast replacements and minimize operational disruptions.
For complex repairs, involving qualified technicians with specialized training in packaging equipment is advised. click this site They possess the know-how to detect problems precisely and carry out fixings efficiently. In addition, recording all fixing activities and parts substitutes is vital for maintaining a detailed upkeep history, which can assist in future troubleshooting.
Lastly, executing a positive technique, consisting of routine examinations and anticipating upkeep methods, improves the dependability of product packaging makers. By adhering to these finest practices, companies can guarantee optimal maker efficiency, minimize operational risks, and extend tools life-span.
Verdict
In final thought, a thorough understanding of packaging maker parts and effective maintenance techniques is crucial for optimum efficiency. By applying these practices, organizations can guarantee the durability and effectiveness of product packaging devices, ultimately contributing to enhanced operational productivity and reduced costs (packaging machine repair service).
Reliable maintenance of product packaging makers pivots on a complete understanding of their vital parts, consisting of the structure, drive system, and securing devices.Reliable operation of packaging machines relies greatly on regular maintenance to avoid common issues that can disrupt manufacturing.Applying preventative upkeep approaches is vital for sustaining the effectiveness and weblink dependability of product packaging equipments. In addition, maintaining exact documents of maintenance activities aids in tracking the machine's efficiency over time, helping with informed decision-making regarding future upkeep needs.
